Before we go over the different types of flanges available, we must understand what makes them unique. Flanges are made of various materials that have varying properties, and each has a specific purpose. It is also important to understand how these flanges are used and which ones are suitable for certain applications. The basics of flange design are described below. There are several types of flanges, including weld neck pipe flange, slip-on flange, and IX seal ring.
Stainless Steel Lap Joint Flange
Stainless steel lap joint flanges are used in the process industry to attach a pipe to a larger diameter. They feature two parts: a backing flange and a stub end. They are available in a wide variety of sizes, material grades, and designs. This article will discuss how to choose the right flange for your needs. Also, learn about the different advantages and disadvantages of stainless steel flanges.
The main benefit of a Lap Joint flange is its ease of installation. Unlike many other types of flanges, you won’t need to filet weld the plates. This allows you to save money upfront by reducing installation time. Lap Joint flanges also offer salvageability if they have to undergo high-corrosion or erosion processes. If this type of flange fails, you can simply replace the Stub End. You can also use a Lap Joint flange with an Angle Ring to achieve the same purpose.
If you’re looking for a high-quality Stainless Steel Lap Joint Flange, you can choose from ANSI, ASME, and BS standards. For example, if your pipe is going to be exposed to harsh environments, you’ll want to choose a 4-inch van stone flange. They’re perfect for a variety of environments. These types of flanges are widely used in the process industry, and the largest suppliers are located in Asia and the Middle East.
Weld Neck Pipe Flange
Weld neck pipe flanges have two basic types: welded and slip-on. Among them, welded necks are generally stronger and can last longer. Slip-on flanges are attached to the pipe by two fillet welds, one at each end. The thickness of the pipe’s wall plus three millimeters is used to protect the flange face. If you’re looking for a weld neck flange, you’ll want to read up on these basics.
The first thing you should know about welding neck pipe flanges is that they need to match the pipe schedule. This schedule dictates the size of the bore. It’s important to keep in mind that a pipe with a larger bore diameter will have less flow. Similarly, the weld neck pipe flange should fit with the pipe schedule, otherwise, the flange will be too thick. The flange will fit almost flush with the pipe, so it won’t have a protruding edge.
Weld neck pipe flanges come in a variety of sizes and shapes. In addition to a weld neck, there are ring joints and tongue and groove flanges. A ring joint is another type, which is used when two pipes have different diameters and require the flange to transfer stress to the pipe. The last type is called slip-on. As its name suggests, it’s linked to the pipe by two fillet welds.
Slip-on Flange
You may be wondering what a slip-on flange is. A slip-on flange is a flange that has a flat face and is attached to a pipe by a fillet or interval weld. They are usually used for high-pressure systems. If you’re unsure, here’s a brief rundown of what a slip-on flange is and what you can do with it.
A Slip-On flange is made of a forged steel body that slides onto the pipe to be welded. They are inexpensive and easy to install. They are also available as lap-joint flanges. There’s no neck to rest on the pipe, so double welding is required for these connections. Buttweld connections are an option, as well, and are more secure than a slip-on flange.
If you’re unsure about how to choose a flange, consider this demonstration video from Trupply. The video will help you understand the different types of flanges available, how to choose the right one, and how they fit on pipes. While flanges are commonly used, not all types fit every pipe. For best results, you should match your flange design and piping system to ensure long-term performance.
IX Seal Ring
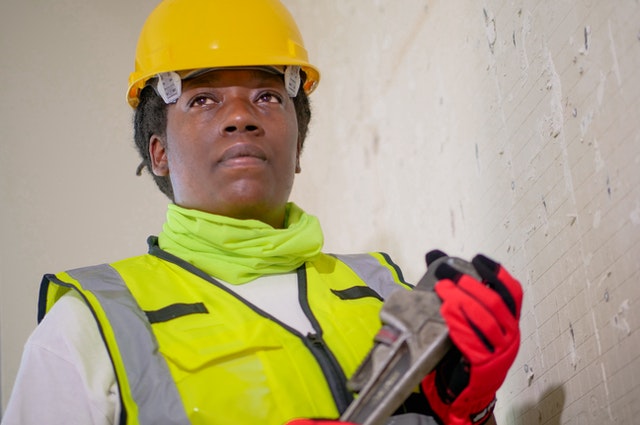
An IX seal ring is a robust elastic ring designed specifically for flanges with NORSOK CFC. It is available in three different sheets of steel and coated with PTFE of various colors. The design of this ring is governed by the geometry of the flange and seal ring, which are oriented towards one another. As a result, it offers a high external pressure capacity while remaining in good alignment.
A seal ring should be designed to withstand the service pressure. It should be made of high-quality material with a minimum yield stress of three hundred and sixty-five MPa. It must be compatible with the design temperature and service medium and must be corrosion-resistant and rustproof. The seal ring should be coated with a layer of PTFE ranging from 10mm to thirty mm thick. The color of the coating must match the requirements given in the following table.
An IX Seal Ring can be used with various types of Norsok Compact Flange connections. These seal rings are color-coded to avoid corrosion. The NORSOK CFC certification of these rings ensures their reliability. An IX Seal Ring is designed to meet all the requirements of NORSOK CFC and NORSOK flange connections. A high-quality seal ring will not cause any damage to flange surfaces.
Slip-on Flanges
If you are looking for slip-on flanges for your process, you’ve probably already heard of JIS standards. These are the standards used for industrial activities throughout Japan. They are coordinated by the Japanese Industrial Standards Committee, which is part of the Japan Standards Association (JSA). Formerly attached to the Ministry of Economy, Trade, and Industry (METI), the JSA is now an independent foundation with a wide range of programs. In general, the JIS-B flange is characterized by its different dimensions and pressure ratings.
There are two basic types of slip-on flanges, namely, square and round. The former is the most commonly used type of flange. The latter is more durable and has a square cut in the center. They are used in applications where the pressure and temperature are high enough. And because they are designed to be interchangeable, they are particularly useful when multiple components are needed. But you should be sure to check the specifics before choosing a slip-on flange for your process.
A raised face slip-on flange features a small extruded zone at the end. This zone sets the gasket during installation. The gasket seat increases the sealing performance. A raised face slip-on flange doesn’t have a weld bevel, which means that it’s easier to match the pipe to the flange and maintain its proper alignment. If you’re looking for a slip-on flange, you’ve come to the right place.
Weld Neck Flange
A quick primer on weld neck flanges will help you decide which one you need and what to look for when choosing one. These flanges are generally made with a straight-through bore and are available in a variety of sizes. The flange must match the pipe’s schedule, which determines the size of the bore. If the pipe is too thick, the flange will not fit, and vice versa.
A welding neck flange’s strength and life are two-thirds of those of a Welding Neck flange. Its unrestricted flow and low turbulence characteristics make it a popular choice in low-pressure applications. The downside of welding neck flanges is their high price. While they have lower material costs, they are not recommended for pressure-sensitive applications.
Weld neck flanges can be either tapered or rounded. The taper on a welding neck Flanged pipe provides a gradual distribution of pressure forces. This helps the flange withstand the shock that may occur during high pressures and temperatures. The extra steel material along the transition minimizes mechanical stress. Because they are made of metal, they can resist corrosive chemicals and other potentially harmful materials.
Reducing Flange
The reducing flange is a piping device that reduces the diameter of a pipe. It is composed of two flanges, the reducing flange, and the standard flange. The reducing flange functions like a reducer fitting in that the larger end of flange A is in contact with the standard flange B, while the smaller end is welded to the pipe. Ideally, the flow should flow from the smaller to the larger end.
A reducing flange is available for a variety of pressures and types. It is fixed to a larger flange by welding, gluing, clamping, or reaming the smaller one. It is the cheapest way to mat two different-sized flanges. This type of flange is also commonly used in shipbuilding, oil and gas fields, water systems, power plants, and industrial vessels.
A reduction flange comes in two types: a type 2 flange with threaded holes, and a type 3 reducing ring with through holes for large-bore bolts. Type 2 reducing flanges are used for pipe projects, while type 3 reducing flanges are used for large-bore applications. The ring-type joint on the larger outlet requires a raised face dimension.